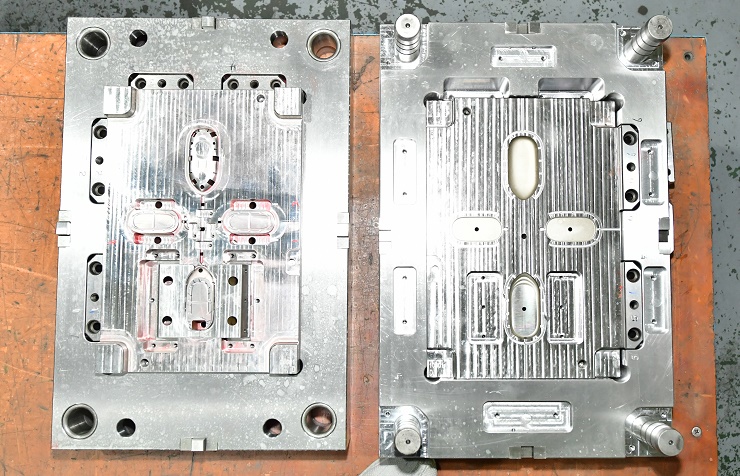
What is Plastic Injection Moulding? (PIM)
Plastic Injection Moulding is a manufacturing process for producing parts by injecting plastic material into a mould. PIM enables parts to be manufactured to a high degree of accuracy in a variety of materials, surface finishes and with a high degree of repeatability.
Many different types of plastic can be used. Each type of plastics have many different grades.
ABS,
Polypropylene (PP),
Polycarbonate (PC),
Nylon (PA-6),
Acetal (POM)
and Acrylic (PMMA)
are all examples of common PIM materials. You will most likely recognize these plastics already. Simple to very complex geometries (shapes) can be created using the Injection Molding process. Plastic resins for PIM are in pellet form. To create a part using PIM we must first create a mold tooling.
Moulds for PIM vary in complexity, this is usually linked to the complexity of the part to be produced. Complex part=Complex mould.
Complex mould=Higher Cost
Moulds can be made using Steels and Aluminium.
Steels used could be P20, H13, NAK80.
Aluminium for mould making is generally aircraft grade. 7075 for example.
In order to manufacture the Mould Tool we first need finished 3D CAD data that represents the finished part.
The Mould Tool is precision designed and engineered and is suitable only for producing parts for the specific CAD data used.
For example, a CNC machine can produce a wide range of parts of varying design and in a wide range of materials. A mould tool is a custom made tool that is capable of making many thousands or millions of the same part in the same material.